生产信息系统(Production Information System – PIS)是为解决生产制造监管痛点而开发的精益信息管理平台,具有设备数采、状态监控、绩效/报警分析、程序管理、设备监控等标准功能模块,亦可功能定制。助力生产信息透明化、精益化流程管理和决策制定,提高生产效率。
生产信息系统(PIS)介绍
同许多生产制造企业的生产管理负责人一样,某电机加工制造工厂的负责人王经理总有这样的疑惑,看着工人将一个个加工完成的工件从机床上搬下来、在工单上进行记录、之后再次装夹、启动机床,觉得这些机床就好像一个个“黑盒子”,让人很难摸清它们“活儿干得到底怎么样?是在满负荷工作,还是在‘偷懒’?”
根据人工统计的数据,王经理所管理车间的设备利用率高达95%,没有进一步提升的空间了。事实真是如此吗?而且工厂当时订单持续旺盛,不增加产能的话,马上就要满足不了订单交付,但工厂场地有限,已经没有空余场地新增设备,难道只能眼睁睁看着新订单流到友商手中吗?
另外,随着市场需求发展,该企业生产产品的更新周期越来越短,产品品类越来越多。这也给加工程序(NC程序)的管理带来很大挑战:
工艺人员要手工管理种类众多、且涉及多个工序的零件加工程序,同时这些加工程序还有众多版本。在日常工作中,很可能因为一些疏忽导致没有使用正确的加工程序。同时,工艺人员在确定正确的加工程序后,还需要将加工程序传输到对应的机床上。因为设备没有联网,因此只能通过优盘拷贝的方式一个一个地将加工程序拷入相应设备,这也是非常容易出错的一个耗时耗力的过程。在加工过程中,操作工如果发现程序编写得有不合适的地方,再找工艺人员进行调整,又得重新拷贝。如果自行调整,看似节省时间,但也可能出现不受控的加工程序版本。
为了解决生产管理部门面临的上述痛点,生产信息系统(PIS)通过不同的功能模块来解决不同环节的问题。
1. 打通数据通路
打通设备数据通路是一切信息化的基础。
在生产制造企业,存量自动化设备所使用的控制器,种类繁多、品牌丰富,而且年代不一。控制器涵盖PLC、数控、机器人、工控机、专用控制器等等。有些在数据通讯方面十分封闭,每个品牌几乎都有自己的通信接口协议。而且即便同一个品牌,不同型号、不同年代的控制系统,其支持的通信接口协议也不同。同时,车间中还有众多老旧设备,有些根本没有以太网接口;有接口的老设备(比如西门子早期SINUMERIK 840D pl系列数控系统),因处理器能力有限,采用市场上一些数据采集方案后,机床操作的反应变慢,拖慢了生产节奏。
PIS在数据采集方面采用西门子工业IoT网关软件(BFC),在车间设备和PIS系统之间建立数据连接。这一标准化的网关软件不仅可以采集西门子SINUMERIK ONE/840D/828D等数控机床的数据,还可以采集第三方数控系统、以及西门子S7系列PLC和第三方PLC的数据。
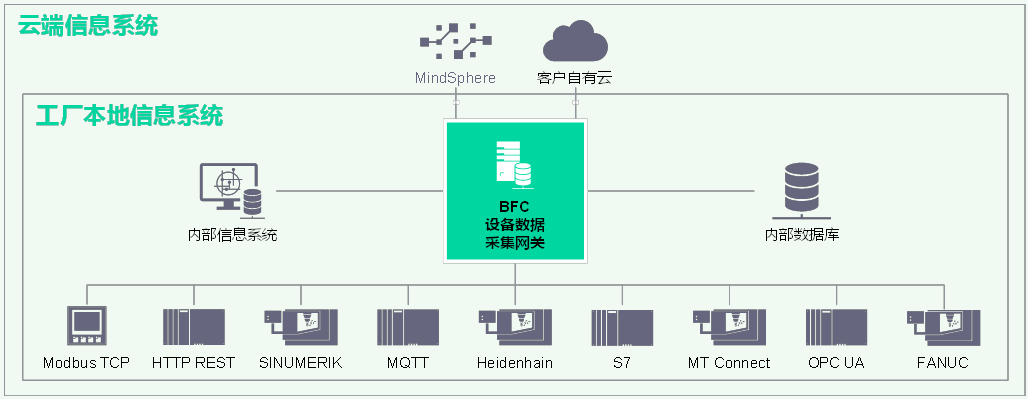
针对西门子SINUMERIK 840D pl这样的老设备,BFC特有的设备资源占用率低的特点,不会让设备采集数据后出现卡顿、反应慢的问题。另外,作为一款标准化的软件网关,BFC具备简单易用的配置页面,用户经过培训后可自行完成采集参数的配置和调整,无需代码级知识。
2. 打开车间的“黑盒子”
有了设备的实时数据,PIS的“设备状态监控与评估分析” 模块(MDC)会对这些数据进行分析和可视化展示,实时呈现不同机床的运行状态和利用率等关键信息,实现生产信息透明化。
在生产精益部门的配合指导下,通过PIS系统的客观数据分析,王经理该发现车间的实际设备利用率是64%,远没有达到之前人工统计的95%,还有很大的提升空间。
随后,王经理协调生产管理人员和精益专家、设备操作人员和维修部门,通过PIS系统、结合生产过程,重点分析设备停待机原因。比如,找出对利用率损失影响大的因素,评估并找到解决方案,从而减少、甚至消除由此导致的停机或待机,从而提高设备利用率。
随着一些列精益改善措施的落地,在系统上线部署6个月后,该企业机加工车间的设备综合利用率从64%提高到75%。由此带来了超过200万元的生产效益增长,工厂对客户订单的交付期也得以缩短,市场占有率得到一定提升。
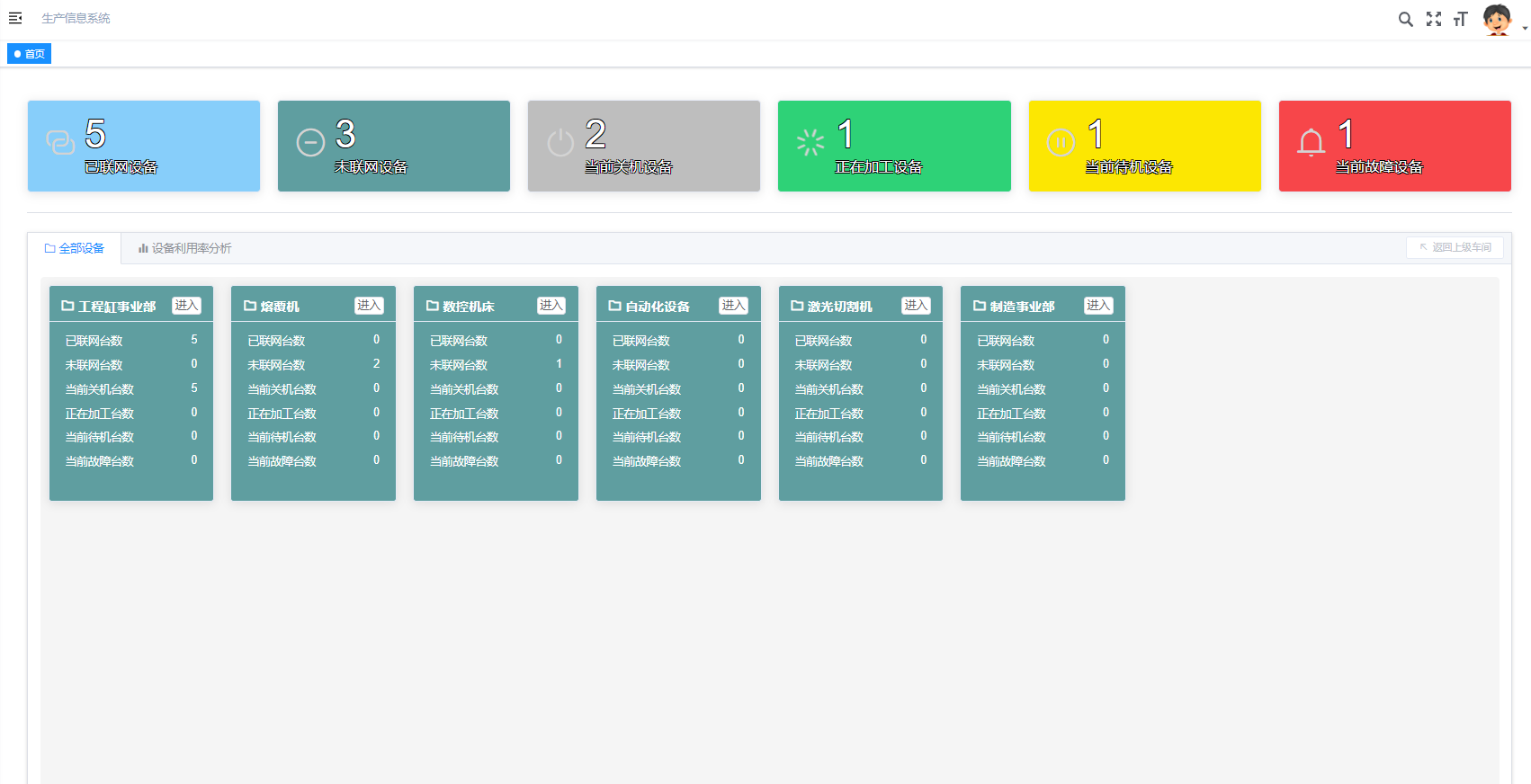
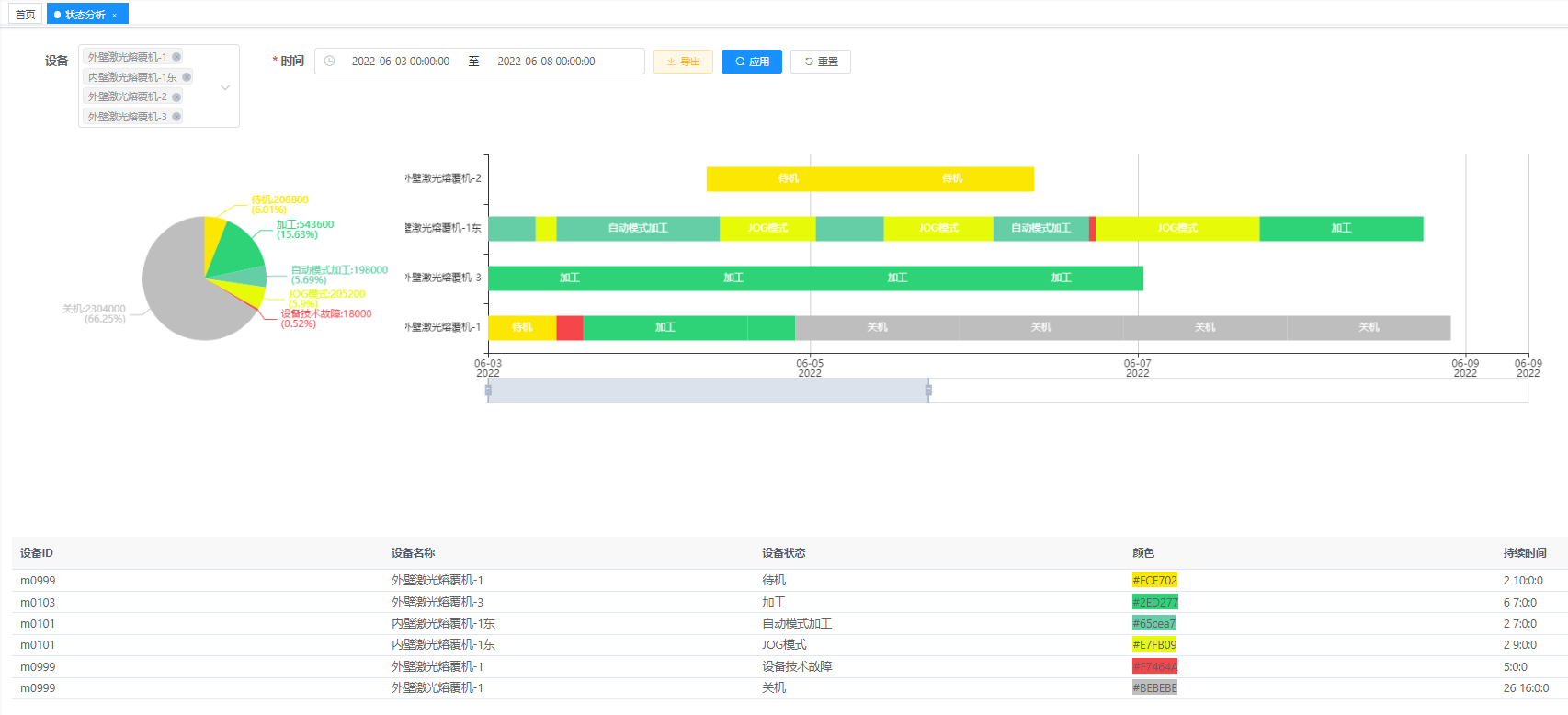
3. 从IT工具到管理流程
针对该企业在数控机床加工程序管理方面所面临的巨大挑战,PIS的“工艺文件传输和管理” 模块(DNC)把所有的数控加工程序和工艺文件(含配套图纸、装夹视频、刀具清单、作业指导书等)都集中保存在工艺服务器中,方便位于办公室的工艺员对加工程序和工艺文件进行统一管理。
工艺员可以按工件类型对加工程序进行分类管理,还能在系统的支持下对加工程序进行版本管理、文件对比和下载审批流程设置等工作。特别是对于工厂内有大量使用相同加工程序的机床,工艺员可以通过“批量下载”的功能一键将程序下发到多台机床上,极大地提高了工作效率。
机床操作员亦可在机床端配置的“DNC终端”平板触屏工控机支持下,查看在线工艺文件,完成相应的确认操作。DNC也通过项目定制,实现同MES的工单管理实现联动。
依托于PIS的DNC模块,该电机加工制造工厂重新梳理、并制定了新的工艺文件管理流程。之前虽然也有流程文件,但因为都需要人工执行,无法监督和管理执行效果。在PIS这一IT软件平台的支持下,新的流程不但执行起来更加简易高效,而且基本排除了人为干扰因素,使得流程不光能上墙,还能落地。
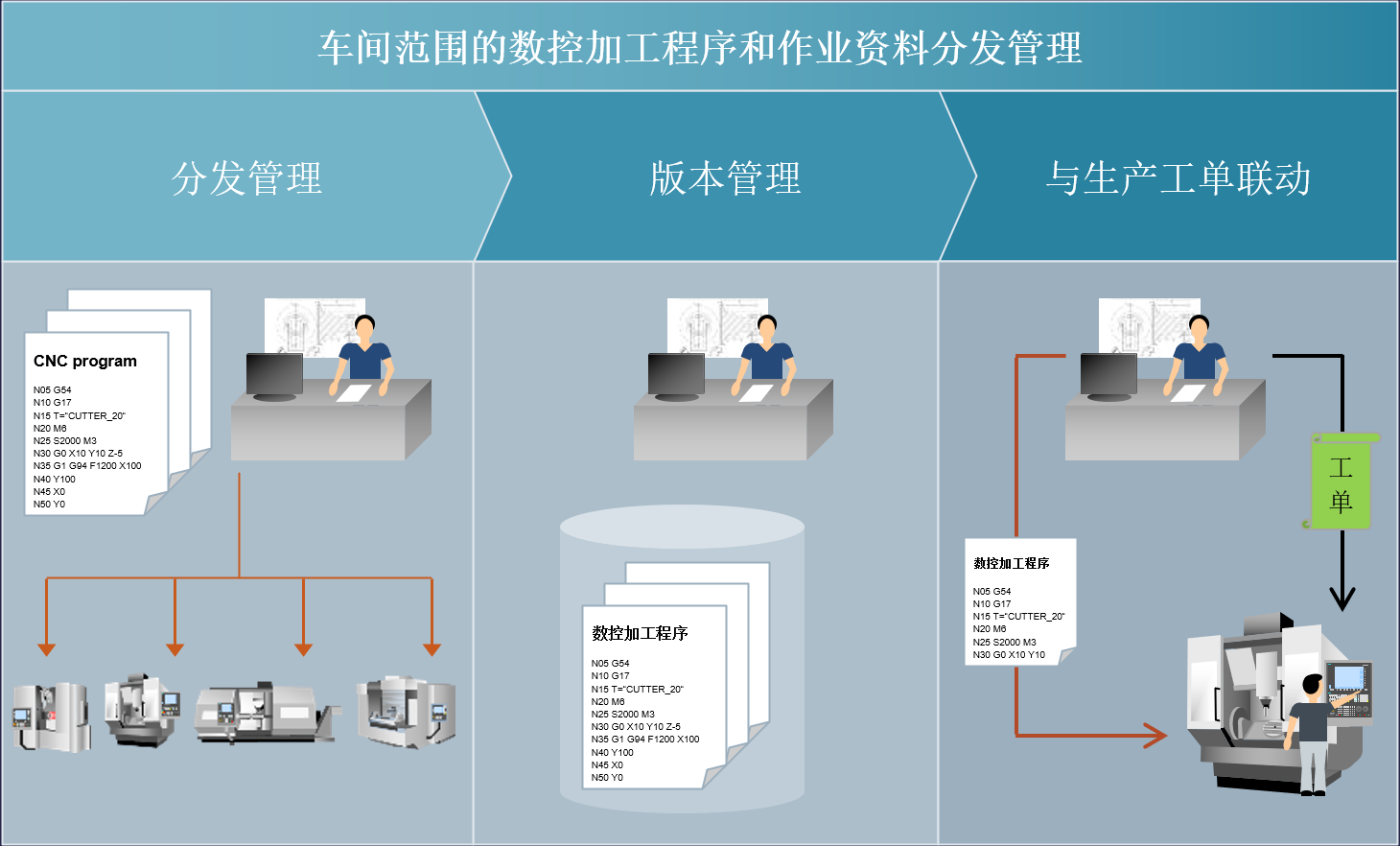
4. 提升全员信息透明度,高效协同
如果每个人都不能充分获得与自身工作相关的信息,也就谈不上有效协同,更不要说高效协同。在非数字化时代,车间内各个工作角色之间的信息传递是零散且低效的,虽然一些工厂使用了看板等精益化的手段来协同。但传统的手段在信息传递的数量、质量和时效方面都相对较低,这也导致了管理人员和员工,特别是一线员工无法更好地主动协同。
PIS的数据可视化大屏功能,可以将生产、设备等相关信息,通过高可读性的可视化图表实时地展示给相关人员,使不同角色的人员都能一目了然地获取工作相关信息,提升协同工作效率。除了可满足大多数需求的标准大屏视图外,我们还可以根据客户需求提供定制化的大屏视图。
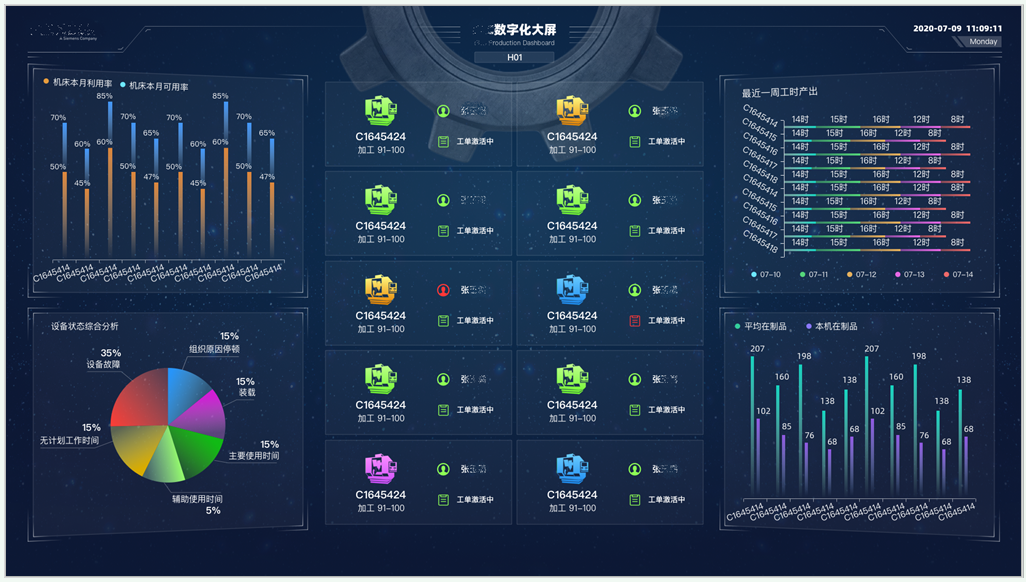
5. PIS系统还能解决什么问题?
除了以上的标准模块以外,PIS还可以根据客户的具体需求提供定制化的功能模块。包括:
实现机床内刀具数据的集中监控,包括刀具名称、尺寸数据、寿命数据等。配合必要的刀具管理流程,在TDM的支持下,刀具部门可优化刀具管理模式。例如基于预设的预警、报警阈值,提醒刀具部门及时更换/配送刀具;亦可与MES的生产工单的联动操作,生成刀具调度清单、并发送给刀具部门作为备刀参考依据;也可与调刀仪进行对接,接收来自调刀仪的刀具尺寸等数据;也可通过刀具RFID改造,实现刀具数据从刀具室、调刀仪到数控机床之间的自动传输;或可建立刀具仓库管理系统。
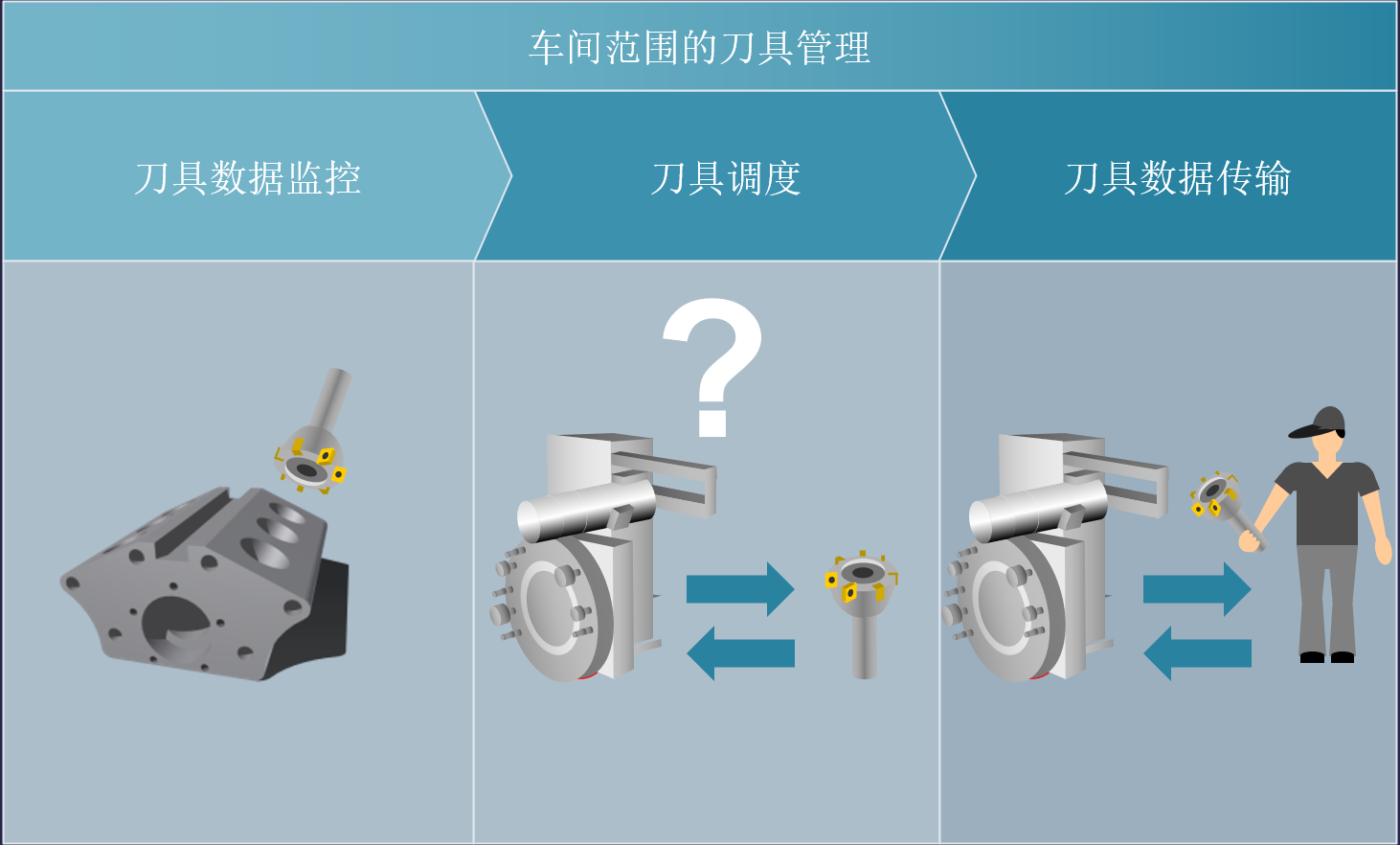
通过以太网远程监视车间内数控机床的实时操作界面,同时在满足一定安全条件下,可对数控机床进行远程操控。
这一功能不仅可方便生产部门集中监控设备状态、生产情况等实时信息,还能在中控室远程监视和操作单台设备。支持维修部门进行设备远程诊断;工艺部门进行设备远程调试;生产部门进行生产远程指导等。配合车间的自动化改造、视频监控系统,更可以减少一线生产人员,降低工人的劳动强度,对EHS进行改善。
在华中区某交通行业制造企业,某个工序单件加工时间接近8小时,之前生产操作人员只能一直在现场监控整个加工过程,几乎没有实质性的工作却又不能离开。在应用PIS的RMC模块后,配合设备视频监控,该企业在中控室就能集中监控所有设备的加工情况,减少了30%的一线生产人员配置。
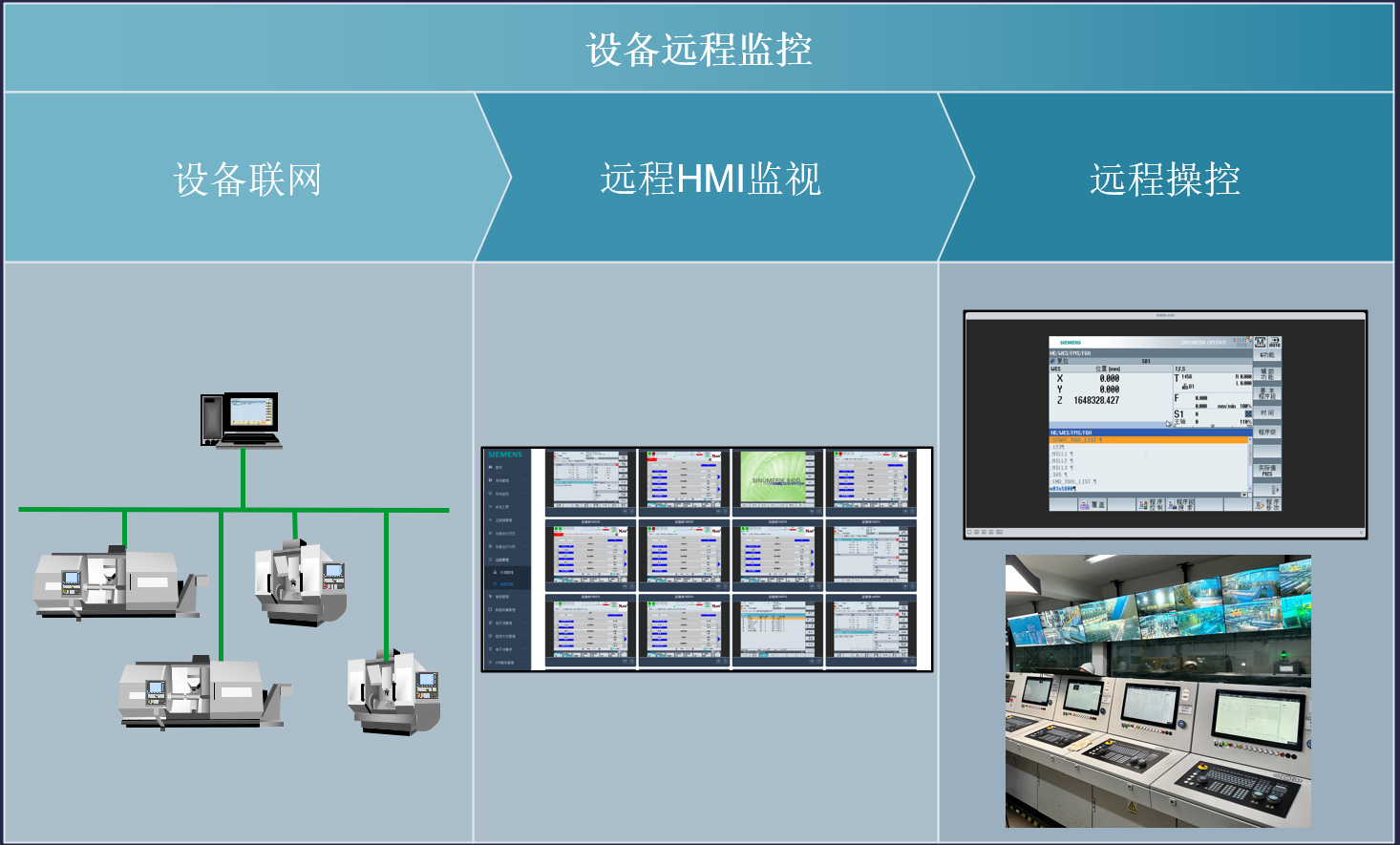
同“设备状态监控与评估分析” 模块(MDC)相似,通过实时采集自动化设备在生产过程中产生的工件过点信息、质量数据和生产过程数据,获得产品生产履历和相关质量报告。进而帮助生产部门、质量部门实现对生产产品的产品追溯、质量分析,甚至可实现可疑件的剔除、产品定位等功能,从而提高生产管理效率和品质把控。
“生产和质量管理模块”的实现,有赖于设备供应商提供的设备接口信号,例如需要在设备自动化控制器中提供必要的工件识别码、设备编号、工件过点信息(入站时间、加工开始时间、加工结束时间和出站时间)、质量合格信息、质量数据、生产过程数据等。一般适用于自动化程度高的自动化生产线,并需要预先同设备供应商配合制定接口规范,提供工件识别传感器,如工件二维码扫描枪。
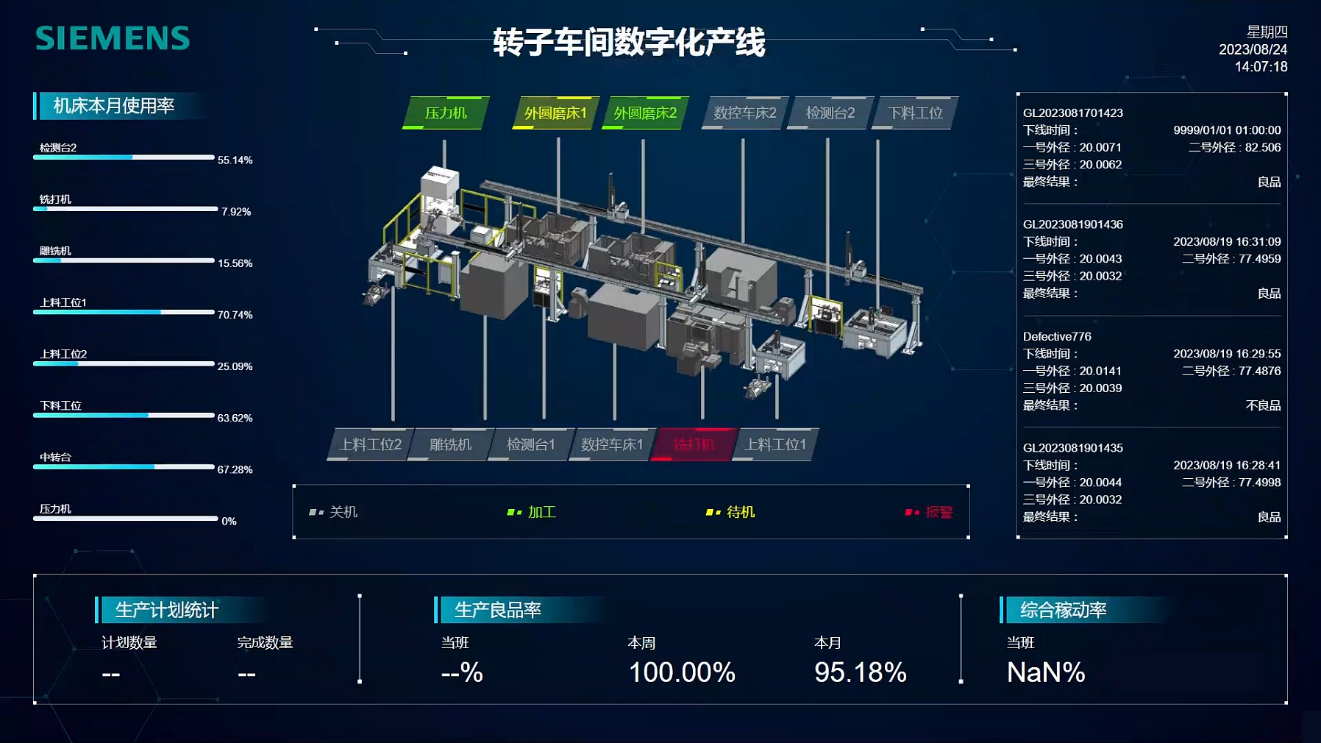
通过采集来自生产设备、生产线或车间安装的能耗仪表的能耗数据,包括水、电、气/汽等,实现对生产过程能耗数据的实时监控,并进一步进行统计分析,从而实现能耗透明化。
通过能耗透明化,助力生产部门或动力部门便于对生产过程的能耗进行实时监控,寻找潜在的监控薄弱点,杜绝跑冒漏的现象;同时定位能耗大的设备和工艺点,进行重点分析,针对性的采取节能减排措施,从而降低能耗、实现成本节约。
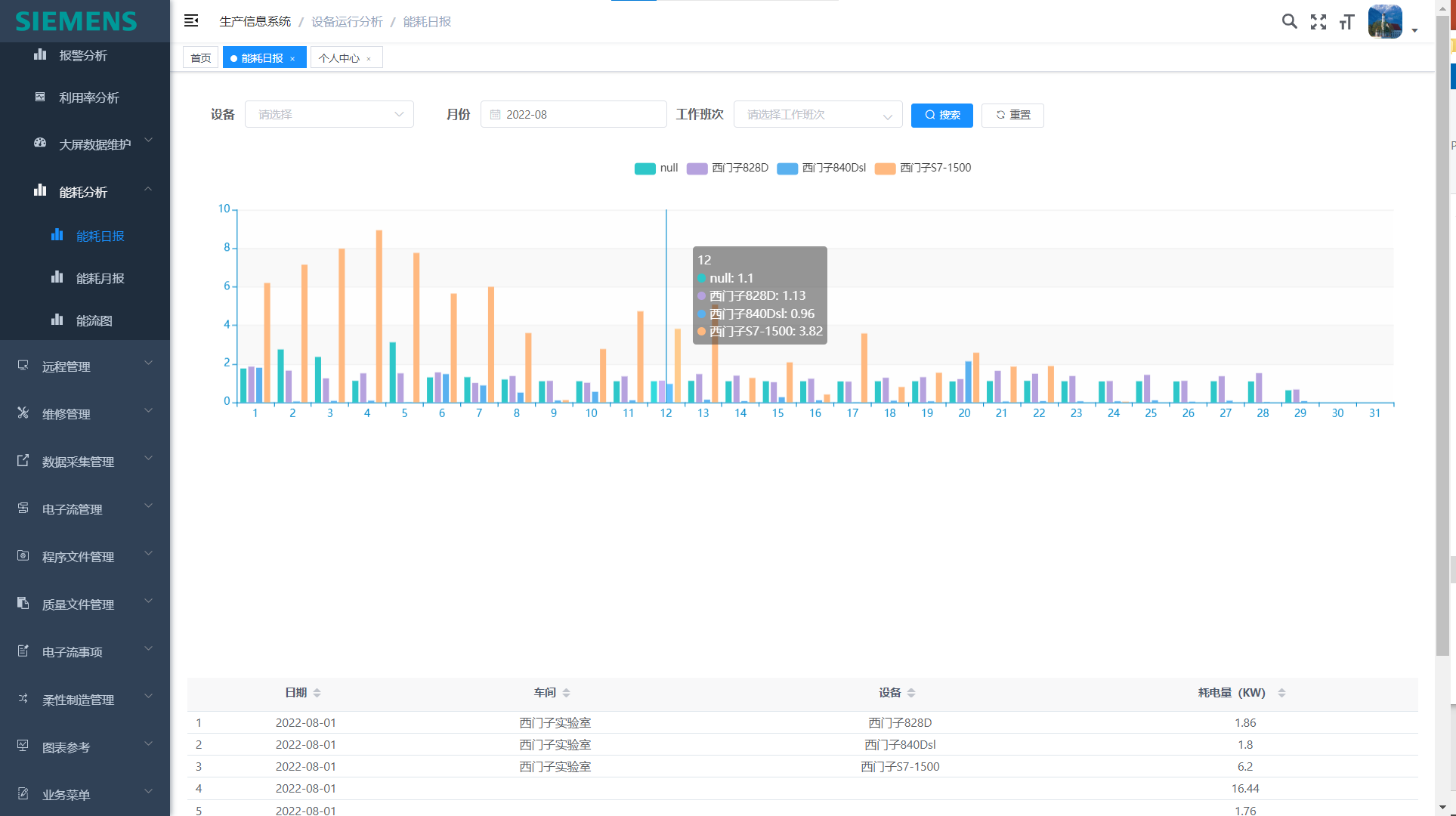
根据客户项目定制、或第三方信息化系统的特殊需求,可提供标准的、或项目定制的通讯接口,以便实现与第三方信息化系统的数据交互。
包括提供相关数据给上层信息化系统,如MES系统;也可支持同上层系统数据交互。
下载生产信息系统选型样本:生产信息系统选型样本.pdf
下载生产信息系统简介:生产信息系统简介.pdf
下载生产信息系统用户介绍手册:生产信息系统用户介绍手册.pdf
扫码分享